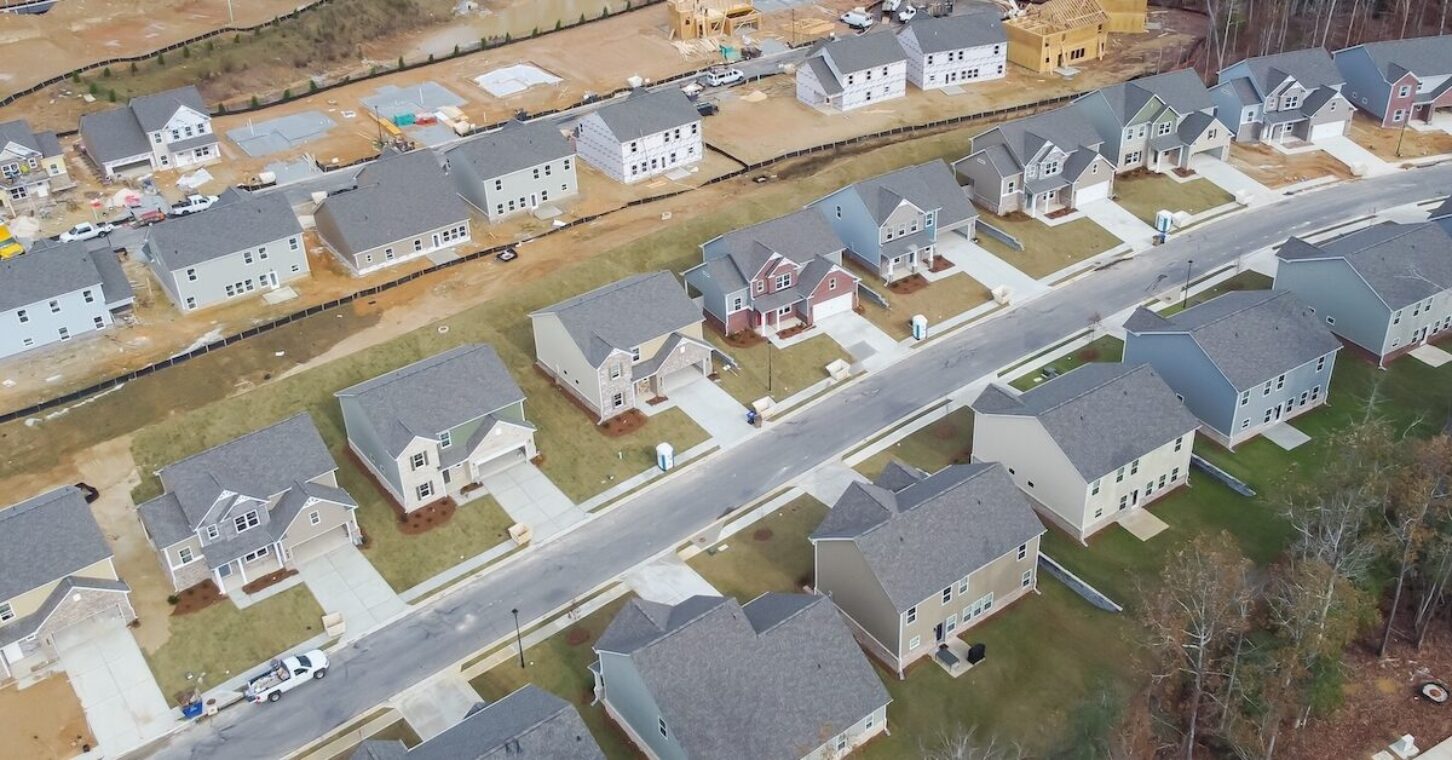
If nothing changes, nothing changes. That truism helps explain what ails our housing market.
Home affordability lags in Georgia (and elsewhere) because of too little supply. The exact size of the shortage is debatable, but here’s a reference point: Georgia added about as many homes between 2010 and 2019 as it did between 1995 and 1999, despite welcoming 2 million new residents in between.
In any case, the size of the problem can be measured in the hundreds of thousands. Yet, the number of new homes built in Georgia last year was still about 30% below the peak from 2005.
So, we still haven’t stopped digging the hole we’re in, much less begun filling it. If you think we’re going to solve the problem just by doing more of what we’ve been doing, or even doing it faster, guess again. It will take that, yes – as well as a willingness to approach things differently.
This different approach includes how we build homes, and from which materials. And that brings me to the unique open house I attended earlier this month in southeast Atlanta.
This open house was not directed at homebuyers, but at government officials and industry partners. While the home at 515 McWilliams Road will be listed for sale soon, the goal that day was to open eyes to a different way of building homes.
You see, this house was a CrossMod home: an industry term for a “crossover, modern” manufactured home. It was built in a factory and brought in on a truck, but this is not your Cousin Eddie’s doublewide.
This home has a porch, a deck and a garage; an open concept living area; three bedrooms and two bathrooms; drywall on the inside and curb appeal on the outside. It’s about 1,750 square feet, sits on a permanent foundation and qualifies for a conventional 30-year mortgage.
It was also built, from start to finish, in just 95 days. What’s more, the developer plans to list it for less than $400,000 – tens of thousands less than the site-built home next door that’s already on the market.
“I think with site builders and their costs today, it really makes it hard to ‘pencil out’ the numbers,” said developer Erick Mulicandov with Atlanta-based Iron Horse Communities. “With interest rates rising, these houses, because their sticker price is a considerable amount less, it gives that flexibility and that freedom to bring an affordable product into the marketplace.
“Also, the time. The time it takes to get a site-build completed is much greater than a manufactured house.”
It is believed this particular house is the first example of an urban in-fill home using this building style and technique. And here we return to the housing shortage issue.
Clayton Homes, the manufacturer of this particular house, builds these types of homes at 12 of its factories (though not yet in Georgia). There are nine other companies manufacturing homes in Georgia.
Those time frames and dollar figures could be key to filling the housing hole we’ve dug ourselves.
What stands in the way? There remains a stigma about manufactured housing dating back decades, even though the industry has come a long way in terms of safety and aesthetics. But that stigma doesn’t only affect buyers.
“One of our challenges has been gaining zoning allowances for CrossMod and off-site built homes,” said Ramsey Cohen, director of industry and community affairs at Clayton Homes. “Our industry is working closely with municipalities across the country to educate community leaders and the public on CrossMod homes and ensure the right zoning allowances are in place.”
Atlanta is more accommodating, Cohen said, allowing manufactured homes within the city limits if they are attached to a permanent foundation as CrossMod homes are. That policy may ultimately give the city a leg up in filling its housing shortage.
Other jurisdictions would be wise to follow suit and allow the kinds of innovations needed to improve housing affordability.